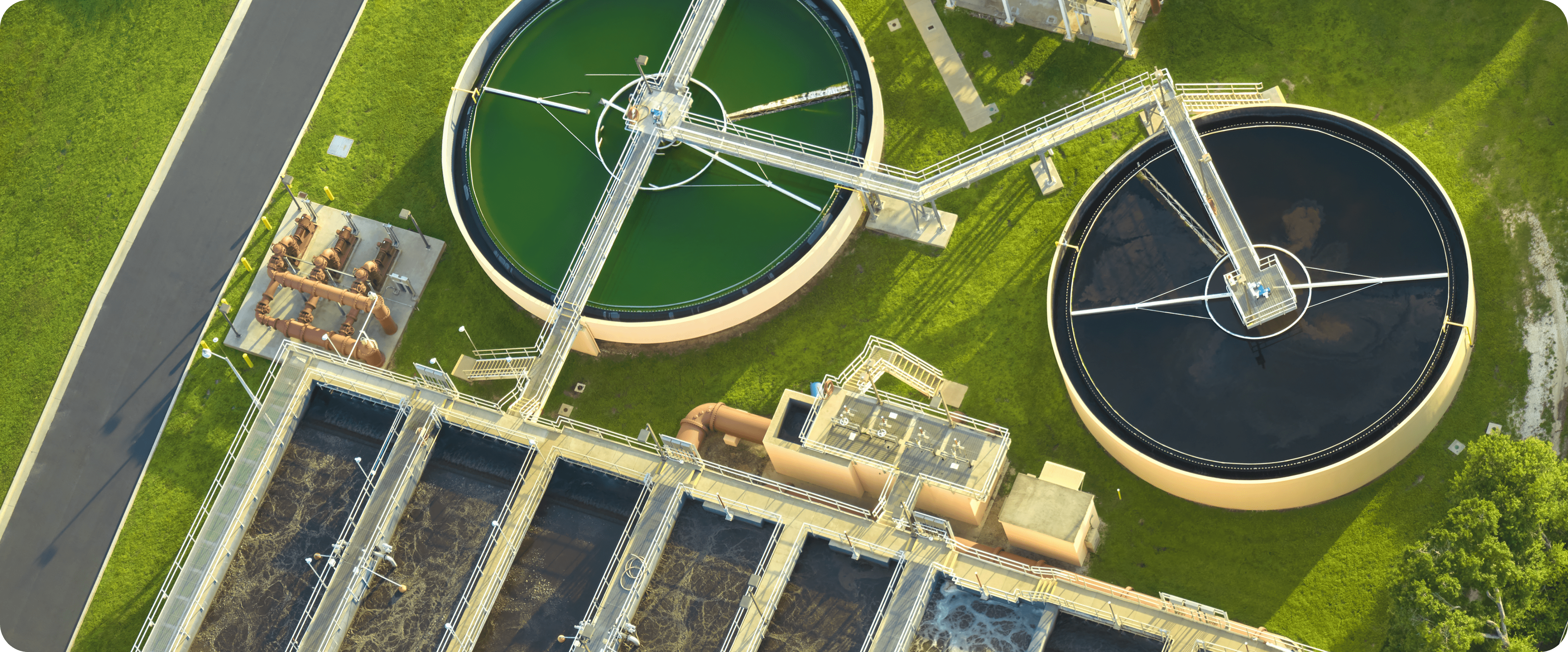
Electromagnetic flow meters (or magmeters) are a type of velocity or volumetric flow meter that operate pursuant to Faraday’s law of electromagnetic induction – which states that a voltage will be induced when a conductor moves through a magnetic field. Magmeters can detect the flow rate of conductive fluids only. Early magmeter designs required a minimum fluidic conductivity of 1-5 microsiemens per centimeter for their operation. The newer designs have reduced that requirement a hundredfold to between 0.05 and 0.1.
An electromagnetic flowmeter consists of a non-magnetic pipe that is lined with an insulating material. A pair of magnetic coils is situated as shown in Figure 1, and a pair of electrodes penetrates the pipe and its lining.
If a conductive fluid flows through a pipe of diameter (D) through a magnetic field density (B) generated by the coils, the amount of voltage (E) developed across the electrodes--as predicted by Faraday's law--will be proportional to the velocity (V) of the liquid. Because the magnetic field density and the pipe diameter are fixed values, they can be combined into a calibration factor (K) and the equation reduces to:
E = KV
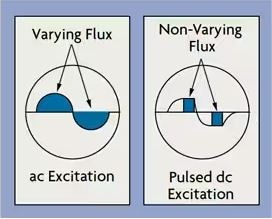
The velocity differences at different points of the flow profile are compensated for by a signal-weighing factor. Compensation is also provided by shaping the magnetic coils such that the magnetic flux will be greatest where the signal weighing factor is lowest, and vice versa.
Manufacturers determine each magmeter's K factor by water calibration of each flow tube. The K value thus obtained is valid for any other conductive liquid and is linear over the entire flowmeter range. For this reason, flow tubes are usually calibrated at only one velocity. Magmeters can measure flow in both directions, as reversing direction will change the polarity but not the magnitude of the signal.
The K value obtained by water testing might not be valid for non-Newtonian fluids (with velocity-dependent viscosity) or magnetic slurries (those containing magnetic particles). These types of fluids can affect the density of the magnetic field in the tube. In-line calibration and special compensating designs should be considered for both of these fluids.
Magmeter Excitation
The voltage that develops at the electrodes is a millivolt signal. This signal is typically converted into a standard current (4-20 mA) or frequency output (0-10,000 Hz) at or near the flowtube. Intelligent magnetic transmitters with digital outputs allow direct connection to a distributed control system. Because the magmeter signal is a weak one, the lead wire should be shielded and twisted if the transmitter is remote.
The magmeter's coils can be powered by either alternating or direct current (Figure 2). When ac excitation is used, line voltage is applied to the magnetic coils. As a result, the flow signal (at constant flow) will also look like a sine wave. The amplitude of the wave is proportional to velocity. In addition to the flow signal, noise voltages can be induced in the electrode loop. Out-of-phase noise is easily filtered, but in-phase noise requires that the flow be stopped (with the pipe full) and the transmitter output set to zero. The main problem with ac magmeter designs is that noise can vary with process conditions and frequent re-zeroing is required to maintain accuracy.
In dc excitation designs, a low frequency (7-30 Hz) dc pulse is used to excite the magnetic coils. When the coils are pulsed on (Figure 2), the transmitter reads both the flow and noise signals. In between pulses, the transmitter sees only the noise signal. Therefore, the noise can be continuously eliminated after each cycle.
This provides a stable zero and eliminates zero drift. In addition to being more accurate and able to measure lower flows, dc meters are less bulky, easier to install, use less energy, and are most cost-effective than ac meters. One new dc design uses significantly more power than the earlier generations and thereby creates a stronger flowtube signal.
Another new design uses a unique dual excitation scheme that pulses the coils at 7 Hz for zero stability and also at 70 Hz to obtain a stronger signal. Magmeter transmitters can be supplied with either ac or dc power. A two-wire, loop-powered dc magnetic flowmeter is also available in an intrinsically safe design, but its performance is reduced because of power limitations.
Pulsed ac meters have also been introduced recently, eliminating the zero stability problems of traditional ac designs. These devices contain circuitry that periodically disrupts the ac power, automatically zeroing out the effects of process noise on the output signal.
Today, dc excitation is used in about 85% of installations and ac magmeters claim the other 15% when justified by the following conditions:
- When air is entrained in large quantities in the process stream;
- When the process stream is a slurry and the solid particle sizes are not uniform and/or the solid phase is not homogeneously mixed within the liquid; or
- When the flow is pulsating at a frequency under 15 Hz.
When any of the above three conditions exist, the output of a pulsed dc meter is likely to be noisy. In some cases, one can minimize the noise problem (hold the fluctuations within 1% of setpoint) by filtering and damping the output signal. If more than 1 to 3 seconds of damping is required to eliminate the noise, it is always better to use an ac meter.
Flow tubes, Liners, and Probes
The face-to-face dimensions of flanged flow tubes (lay lengths) usually meet the recommendations of the International Organization for Standardization (ISO). The dimensions of short form magmeters usually meet these guidelines as well. Magnetic flow tubes and liners are available in many materials and are widely used in all the process industries, including food, pharmaceutical, mining, and metals.
Some liner materials (particularly PFA) can be damaged when pry bars are used while installing it or removing it from process piping. They can also be damaged by over-torquing the flange bolts. Liner protectors are available to help prevent such damage.
Any flowtube can generally be used with any transmitter offered by the same manufacturer. Depending on its construction and features, the cost of a 2-in. magnetic flowmeter can range from $1,500 to $5,000. This cost has been coming down but is still higher than that of the least expensive flow sensors.
Magnetic flowmeters also can be packaged as probes and inserted into process pipes through taps. These probes contain both the electrodes and magnetic coils. The flowing process fluid induces a voltage at the electrodes, which reflects the velocity at the probe tip and not the average fluid velocity across the pipe. These magmeters are inexpensive and retractable. Therefore, the process does not have to be shut down to install or remove them. Metering accuracy is highly dependent on the relationship between the measured velocity and the average velocity in the pipe.
Electrodes
In conventional flow tubes, the electrodes are in contact with the process fluid. They can be removable or permanent if produced by a droplet of liquid platinum as it sinters through a ceramic liner and fuses with the aluminum oxide to form a perfect seal. This design is preferred due to its low cost, its resistance to abrasion and wear, its insensitivity to nuclear radiation, and its suitability for sanitary applications because there are no cavities in which bacteria can grow. On the other hand, the ceramic tube cannot tolerate bending, tension, or sudden cooling and cannot handle oxidizing acids or hot and concentrated caustic.
In a more recent capacitively- coupled design, non-contacting electrodes are used. These designs use areas of metal sandwiched between layers of liner material. They are available in sizes under eight inches in diameter and with ceramic liners. Magmeters using these non-contacting electrodes can "read" fluids having 100 times less conductivity than required to actuate conventional flowtubes. Because the electrode is behind the liner, these designs are also better suited for severe coating applications.
Recent Developments
When a magnetic flowmeter is provided with a capacitance level sensor embedded in the liner, it can also measure the flow in partially full pipes. In this design, the magmeter electrodes are located at the bottom of the tube (at approximately 1/10 the pipe diameter) in order to remain covered by the fluid. Compensation is provided for wave action and calibration is provided for full pipe, no flow (static level), and partially filled pipe operation.
Another recent development is a magnetic flowmeter with an unlined carbon steel flowtube. In this design, the measuring electrodes mount externally to the unlined flowtube and the magnetic coils generate a field 15 times stronger than in a conventional tube. This magnetic field penetrates deep into the process fluid (not just around the electrode as with standard magmeter probes). The main advantage is low initial and replacement costs, since only the sensors need be replaced.
Choosing an Electromagnetic Flow Meter
Magnetic flowmeters can detect the flow of clean, multi-phase, dirty, corrosive, erosive, or viscous liquids and slurries as long as their conductivity exceeds the minimum required for the particular design. The expected inaccuracy and rangeability of the better designs are from 0.2-1% of rate, over a range of 10:1 to 30:1, if the flow velocity exceeds 1 ft/sec. At slower flow velocities (even below 0.1 ft/s), measurement error increases, but the readings remain repeatable.
It is important that the conductivity of the process fluid be uniform. If two fluids are mixed and the conductivity of one additive is significantly different from that of the other process fluid, it is important that they be completely intermixed before the blend reaches the magmeter. If the blend is not uniform, the output signal will be noisy. To prevent that, pockets of varying conductivity can be eliminated by installing a static mixer upstream of the magmeter.
Magmeter size is determined by capacity tables or charts published by the manufacturer. Figure 4-3 provides a flow capacity nomograph for line sizes from 0.1 in. to 96 in. For most applications, flow velocities should fall between 3 ft/sec and 15 ft/sec. For corrosive fluids, the normal velocity range should be 3-6 ft/sec. If the flowtube is continuously operated below 3 ft/sec, metering accuracy will deteriorate, while continuous operation exceeding the upper limit of the normal velocity range will shorten the life of the meter.
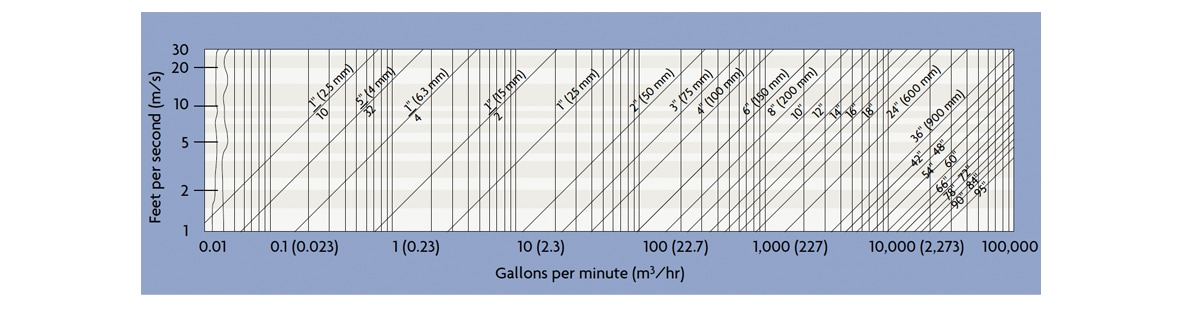
The obstructionless nature of the magmeter lowers the likelihood of plugging and limits the unrecovered head loss to that of an equivalent length of straight pipe. The low pressure drop is desirable because it lowers pumping costs and aids gravity feed systems.
Problem Applications
The magmeter cannot distinguish entrained air from the process fluid; therefore, air bubbles will cause the magmeter to read high. If the trapped air is not homogeneously dispersed, but takes the form of air slugs or large air bubbles (the size of the electrode), this will make the output signal noisy or even disrupt it. Therefore, in applications where air entrainment is likely, the meter should be sized so that the flow velocity under normal flow conditions is 6-12 ft/sec.
Coating of the electrodes is another common magmeter problem. Material build-up on the inner surfaces of the meter can electrically isolate the electrodes from the process fluid. This can cause a loss of signal or a measurement error, either by changing the diameter of the flow tube or by causing span and zero shifts. Naturally, the best solution is prevention. One preventive step is to size the meter such that, under normal flow conditions, the flowing velocity will be relatively high: at least 6-12 ft/sec, or as high as practical considering the possibility of erosion and corrosion.
Another method of prevention is to use electrodes that protrude into the flow stream to take advantage of the turbulence and washing effect. In more severe service, a mechanical cleaning system can be installed and used intermittently or continuously to eliminate coating and build-ups.
Omega Magmeters
Insertion Magmeters
These versatile, simple-to-install flow meters deliver accurate flow measurement over a wide dynamic range in pipe sizes ranging from 0.5 to 8”, satisfying the requirements of many diverse applications. FMG3000 Series magmeters offer a variety of output options for use with Omega flow instrumentation that has a frequency or 4 to 20 mA output. Flow velocity measurement is compensated for temperature via an integrated temperature sensor.
In-Line Magmeters
The FMG90B Series electromagnetic flow meters are designed for measurement of conductive liquids. The FMG90B magmeters have no moving parts and a PTEFE lining, they can handle applications involving wastewater, pulp, food, and slurries.
Low Flow Magmeters
The FMG-2000 has no moving parts, and electrodes are designed to discourage fouling. This magmeter requires no maintenance in applications where debris would impede mechanical meters. There are no parts to wear out. Minimal straight pipe requirements allow FMG-2000 Series meters to be used in piping configurations where there is little space between the meter and an elbow. FMG-2000 Series meters are rated IP68 for applications where the meter may be under water up to a depth of 3 m (10’) for prolonged periods of time. Rate and total indication are standard. Rate and total units and pulse output are settable via the front panel touch key pad by the user.
Installing an Electromagnetic Flow Meter
The magnetic flowmeter must always be full of liquid. Therefore, the preferred location for magmeters is in vertical upward flow lines. Installation in horizontal lines is acceptable if the pipe section is at a low point and if the electrodes are not at the top of the pipe. This prevents air from coming into contact with the electrodes. When the process fluid is a slurry and the magmeter is installed at a low point, it should be removed during long periods of shutdown, so that solids will not settle and coat the internals.
If it is essential to drain the magmeter periodically, it should be provided with an empty tube zero option. When this option is activated, the output of the transmitter will be clamped to zero. Detection of empty tube conditions is by circuitry connected to extra sets of electrodes in the flow tube. The empty tube zero feature can also be activated by an external contact, such as a pump status contact.
Magmeters require five diameters of straight pipe upstream and two diameters downstream in order to maintain their accuracy and minimize liner wear. Liner protectors are available to protect the leading edge of the liners from the abrasive effects of process fluids. If the magmeter is installed in a horizontal pipe exceeding 30 ft in length, the pipe should be supported on both sides of the meter.
The magnetic flowmeter must be electrically grounded to the process liquid. This is because the magmeter is part of the path for any stray current traveling down the pipeline or through the process liquid. Bonding, by grounding the meter at both ends to the process fluid, provides a short circuit for stray currents, routing them around the flowtube instead of through it. If the system is not properly grounded, these currents can create a zero shift in the magnetic flowmeter output.
Electrical bonding to the process fluid can be achieved by metal ground straps. These straps connect each end of the flow tube to the adjacent pipeline flanges, which, in turn, are in contact with the process liquid. Straps are used when the piping is electrically conductive. When the pipe is non-conductive or lined, grounding rings are used. The grounding ring is like an orifice plate with a bore equal to the nominal size (inside diameter) of the flow tube. It is installed between the flanges of the flow tube and adjacent process piping on the upstream and downstream sides. The flow tube is bonded to the process fluid by being connected to the metallic grounding rings, and is grounded by being wired to a good conductor, such as a cold water pipe.