The Rutgers Food Innovation Center is a globally recognized food business that offers everything to support a food business from concept to commercialization. Omega's relationship with Rutgers sprouted with their eager goals in substituting manual processes with an IoT solution that granted them hands-off data collection capabilities.
Challenge
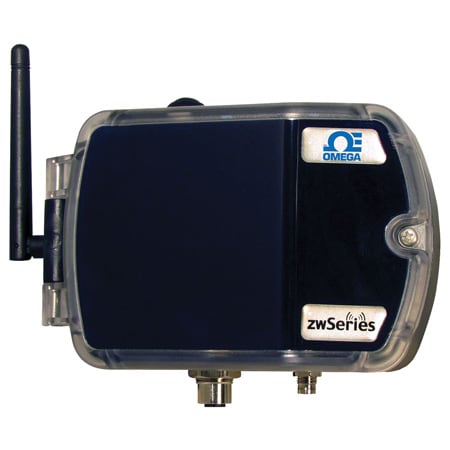
- Inefficient, manual processes for food safety compliance
- Lack of data analytic capabilities
- Missed opportunity for predictive maintenance
The Food Innovation Center at Rutgers University (FIC), is a globally recognized food business incubator and processing facility that supports domestic and global food companies with research and development, marketing and marketing research, quality assurance, and business and food safety training. Additionally, a primary focus of their program is to guide companies through the USDA and FDA compliance and inspection processes. Thus, it’s important to the FIC that they set a gold standard in food safety compliance.
To increase precision in their food manufacturing process and to improve overall food safety compliance, the FIC recently implemented an OMEGA wireless IoT temperature monitoring solution for their kettles and cold storage equipment. While the FIC was pleased with the added temperature precision, there were still other aspects of the food safety compliance process that remained paper-based and not as efficient as they could be.
New FDA regulations also meant that third-party audits were no longer optional, but required. As a result, the FIC needed to document even more of their processes to show compliance.
Finally, with temperature data now being digitally logged, but with no additional data analytic capabilities to draw insights from the data, the FIC recognized that there was a missed opportunity to use the data for additional use cases, such as predictive maintenance.
Solution
- OMEGA PLATINUM series microprocessor-based PID controllers
- OMEGA ZW-ED wireless sensor/transmitter system
- Data Illuminations automated data processing and management solution
Recognizing the compliance challenges the FIC still faced and seeing an opportunity to take their IoT temperature monitoring solution to the next level, OMEGA Engineering worked with the FIC and with a data automation and management firm, Data Illuminations, to develop a holistic, end-to-end automated wireless temperature monitoring and data analytics solution for the FIC.
The first step was to help the FIC eliminate paper-based processes and establish a digital footprint for all compliance documentation. Not only would doing so give the FIC immediate access to the data but by collecting all the data into a centrally managed database, they would have additional capabilities to construct insightful analytical outcomes from the data.
“By integrating Data Illuminations into the system we already had in place, I could get visual, easy-to-read reports based on the data the system was collecting,” says Mellonie O’Neill, Senior Manager: QA Compliance & Training at the Rutgers Food Innovation Center.
As part of the solution, the FIC now has access to a web-based notification center where all the paperwork that needs to be acknowledged to remain in compliance is stored. And now, in addition to receiving temperature alerts, the FIC also receives alerts about compliance documentation tied to the temperature monitoring alerts. For example, if during a production run the kettle gets too hot or too cold, creating a food safety issue, alerts pop up not only about the temperature changes, but also regarding what the QA team needs to document.
Additionally, because the system is web-based, the whole team has access and can see at a glance, even on a cell phone, what the issues are and what needs to be done to maintain compliance, making the process more collaborative and efficient than the previous paper-based system.
Results
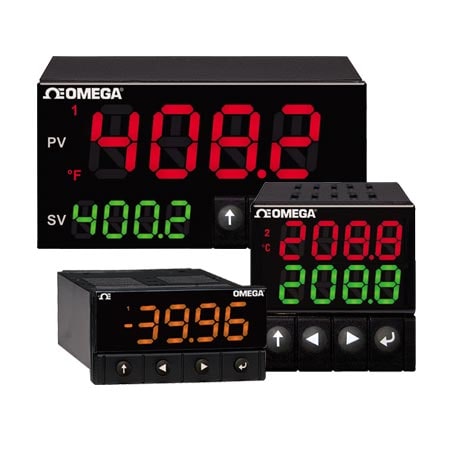
- 25% time savings by eliminating manual processes
- Streamlined food safety compliance process
- Analytical insights for predictive maintenance
For the FIC, the new solution has provided numerous benefits, including:
- Replacing manual processes
- Reducing human errors
- Providing a more proactive approach to maintenance
- Reducing overhead and costs
O’Neill describes the impact of the solution as “tremendous.” Saying, “I can pull up data at any time. It used to be a very time-consuming process to go through the chart records at the end of each week. Now, what took me hours a week takes five minutes.”
In fact, O’Neill estimates that overall, she’s seen a 25 percent time savings in her QA role due to having the data she needs available in real-time in an easy-to-visualize manner.
The data can also help the FIC with predictive maintenance. For example, they now can use the data management software to not only track temperature settings, but to collect data on the temperature sensors themselves. This will allow them to run calculations about maintenance issues and be able to proactively identify issues such as needing to replace the batteries in the sensor or re-calibrate a sensor.
“In the food processing business, it can cost a lot of money if you have to shut down your plant,” says Frank Paytas sales manager at OMEGA Engineering. “So being able to identify issues before they become one is huge – and a big part of the value of an IoT ecosystem.”
Additionally, by digitizing the compliance documentation process and setting up alerts for compliance tasks, the FIC has been able to free up staff time to focus on the business goals rather than task-oriented responsibilities.
“This helps Food Innovation Center clients not only get to market quicker, but scale their products more efficiently, saving on production costs. Their current team can stay the same size even as the facility expands – and they don’t need to hire additional IT,” says Jameson Miller, Founder of Data Illuminations.
“We handhold the entrepreneur through the whole process,” says O’Neill. “We have to know that they are in compliance. We oversee the client’s food safety parameters and have the authority to stop a production run, so having real-time data of our temperatures is important to making sure the process is in compliance and running smoothly.”